Эффективность эксплуатации инструмента определяется сочетанием комплекса требований к камнеобрабатывающему оборудованию, алмазному инструменту и технологии обработки, оптимизированных по отношению к характеристикам камня. Применительно к дисковой распиловке эти требования могут быть сформулированы следующим образом:
1. Относительно оборудования: - параметры точности по радиальному биению вала шпинделя и торцевому биению опорного фланца; - строгая параллельность плоскости опорного фланца относительно плоскости резания; - точность изготовления фланцев, правильно подобранных по диаметру в зависимости от диаметра круга; - мощность электропривода, соответствующая диаметру и количеству кругов на валу; - обороты на валу, определяющие скорость резания в соответствии с твердостью обрабатываемого материала; - возможность регулирования скоростью продольной подачи круга и глубины резания в широких пределах; - система охлаждения, обеспечивающая требуемый расход воды в зависимости от диаметра и количества кругов; - натяжение ремней, отсутствие люфтов и вибраций в шпинделе и т.д.
2. Относительно инструмента: - размеры, тип и конструкция сегментов, их количество на круге, состав по алмазам и связке, правильно подобранный для распиливаемого камня; - допуски по радиальному и торцевому биениям, плоскостности корпуса, его жесткость и правильное натяжение в зависимости от скорости резания и материала; - допустимый уровень динамического дисбаланса круга, исключающий вибрации при работе.
В табл. 1 приведены некоторые основные требования к оборудованию и сегментным кругам в диапазоне диаметров от 300 до 3 000 мм.
Таблица 1. Требования к оборудованию и сегментным кругам 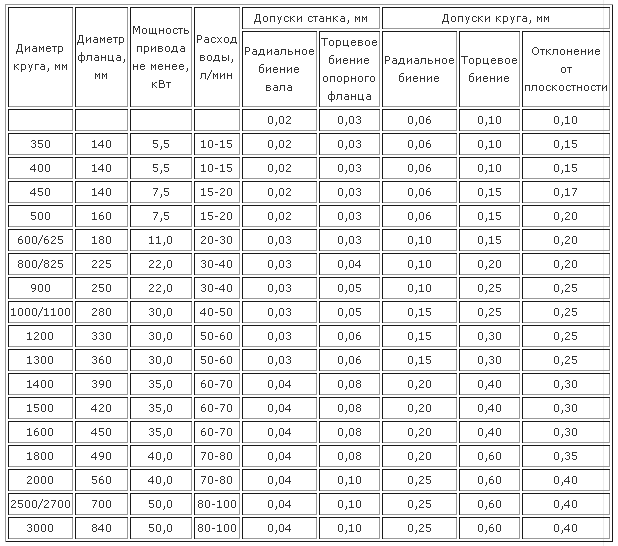
3. Относительно технологии резания: - скорость резания (периферийная) в соответствии с твердостью и классом обрабатываемости камня; - глубина резания и скорость продольной подачи; - оптимальная производительность резания в зависимости от характеристик камня.
Очевидно, что показатель производительности резания является производной величиной от скорости продольной подачи и глубины резания. Однако очень важным при этом является понимание того, что для заданной производительности резания максимальный эффект по ресурсу работы круга достигается при сочетании относительно малых глубин резания с высокими скоростями продольной подачи. При таких условиях обеспечивается мягкое резание в режиме самозатачивания сегментов, эффективнее охлаждается зона резания и выносится шлам, меньше контактная поверхность круга с камнем, что, в свою очередь, снижает нагрузку на круг и шпиндель станка и соответственно меньше энергозатраты.
Современная технология многодисковой распиловки гранитных блоков предусматривает использование скоростей продольной подачи от 10 до 15 м/мин при глубинах резания от 0,5 до 1,5 мм в зависимости от класса обрабатываемости гранита. При однодисковой распиловке, как правило, применяют скорости продольной подачи от 2 до 8 м/мин и глубины резания от 2 до 20 мм. К сожалению, зачастую используемое старое оборудование не позволяет задавать необходимую продольную подачу. Вследствие этого, чтобы выйти на требуемую производительность, камнеобработчики вынуждены работать на глубинах резания от 50 до 300 мм при продольной подаче соответственно от 0,5 до 0,2 м/мин. В таких условиях могут работать круги с утолщенными жесткими корпусами, имеющими широкие межсегментные пазы, оснащенные сегментами на относительно мягкой связке. В конечном итоге, при меньшей производительности ресурс кругов снижается в 1,5-2 раза в сравнении с оптимальными рекомендуемыми параметрами резания для данного класса гранита.
В табл. 2 приведены рекомендуемые режимы однодисковой резки для некоторых наиболее известных типов гранитов Украины и России, разбитых на 3 группы по твердости, содержанию кварца и обрабатываемости.
Нижнее и верхнее значения показателя производительности приведены в таблице как минимальные и максимальные. Ограничение снизу объясняется тем, что при меньших значениях этого параметра процесс распиловки может перейти из режима самозатачивания в режим "засаливания”, что приведет к потере режущей способности круга из-за зашлифовки выступающих кромок алмаза. Ограничение сверху связано с ресурсом работы круга. То есть дальнейшее повышение производительности и соответственно нагрузок, воздействующих на режущую поверхность сегментов, сопровождается преждевременным вырыванием части алмазных кристаллов из связки и его интенсивным износом.
Таблица 2. Рекомендуемые параметры резания для разных гранитов 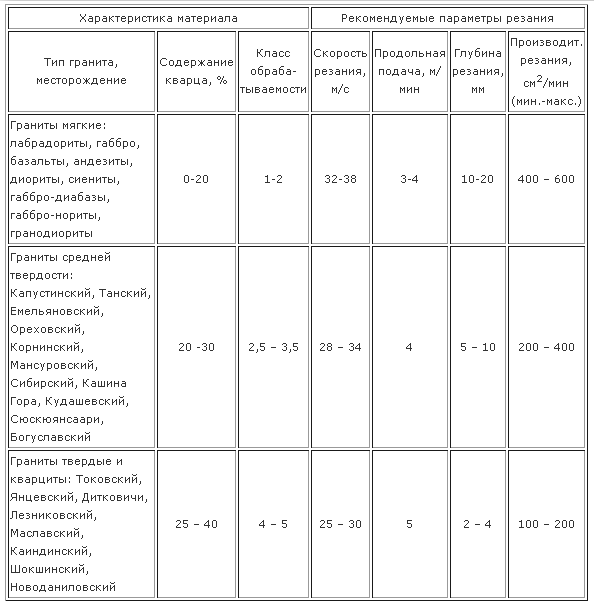
Проведем небольшой анализ с целью правильного понимания качественных взаимосвязей между разными факторами, определяющими результирующий показатель режущей способности алмазного отрезного круга, которая в конечном итоге определяется размерами частиц шлама, образующегося в процессе распиловке. Очевидно, что чем крупнее этот шлам, тем выше его абразивность, вызывающая износ связки и обеспечивающая выступание режущих граней алмазных кристаллов над рабочей поверхностью связки.
В процессе такого анализа влияния разных групп факторов на размер частиц шлама условно примем, что остальные факторы остаются неизменными.
1. Влияние характеристик инструмента: Размер частиц шлама растет: - при увеличении среднего размера зерен кристаллов алмаза; - при снижении содержания алмазов в инструменте; - при повышении средней прочности алмаза; - при снижении твердости и износостойкости связки; - при повышении прерывистости режущей поверхности инструмента.
2. Влияние характеристик обрабатываемого материала: Размер частиц шлама крупнее: - при низкой твердости и повышенной пористости камня; - при низком содержании кварца и с уменьшением среднего размера его включений в структуре камня.
3. Влияние параметров резания: Размер частиц шлама увеличивается: - при снижении периферийной скорости резания круга; - при повышении скорости продольной подачи; - при снижении глубины резания; - при повышении удельной мощности резания.
Таким образом, мы рассмотрели факторы, определяющие производительность процесса распиловки, понимая, что его эффективность характеризуется и ресурсом работы инструмента. Говоря о взаимосвязи этих двух параметров, мы можем утверждать, что существует практически обратно пропорциональная зависимость между производительностью резания и ресурсом круга. То есть, при прочих равных условиях, увеличение производительности в 2 раза будет сопровождаться снижением ресурса в той же степени.
В процессе разработки и постановки на производство новых конструкций алмазного инструмента, составов связок и алмазов инженеры СП "Укр-Диамант” всегда стремятся найти оптимальное соотношение между этими двумя противоречивыми параметрами. В результате такого подхода были предложены новые конструктивные решения по сегментным кругам диаметром от 900 до 1600 мм для многодисковой распиловки гранитных блоков и сегментным кругам для распиловки плит из гранита в диапазоне диаметров от 300 до 800 мм.
В первом случае была предложена конструкция сегментных кругов с узкими межсегментными пазами с повышенной в 1,5 раза режущей поверхностью. Это достигалось тем, что вместо одного сегмента трапециевидной формы типа "сэндвич” длиной 24 мм на каждый стальной "зуб” корпуса напаивалось по два сегмента длиной 18 мм. И хотя стоимость кругов возросла в среднем на 25%, ресурс работы в результате повысился на 55-60%, что в итоге позволило снизить удельные затраты в среднем на 20%.
Для кругов диаметром 300-800 мм вместо стандартных сегментов длиной 40 мм были разработаны сегменты длиной 18 мм и высотой 15 мм, имеющие по одному боковому пазу (углублению) с каждой стороны. В сечении такие сегменты имеют форму, напоминающую букву "S”, и поэтому они названы "S”-образными. Применение кругов с такими сегментами подтвердило их эффективность, особенно при высокопроизводительной распиловке плит из твердых гранитов. При увеличении цены круга на 15-18% его ресурс возрос в 1,5 раза, а удельные затраты были снижены в среднем на 25%.
Следует отметить, что уменьшение удельных затрат на алмазный инструмент в значительной степени зависит и от того, насколько условия обработки, состояние об орудования, квалификация персонала и культура производства на каждом рабочем месте соответствуют современным требованиям.
Резюмируя приведенное выше, можно сказать, что максимальная эффективность процесса обработки камня алмазным инструментом может достигаться совместными усилиями изготовителей и потребителей этого инструмента, способных профессионально решать каждый свою часть этой общей проблемы.
Автор: Арустамян А. С. , канд. техн. наук СП "Укр-Диамант”
|